When 3D printing is Revolutionising the Production of Jewellery
By providing designers with greater creative freedom, 3D printing is revolutionizing how jewellery is designed, produced, and consumed.
By Xiao Qing, 8 Jan 2025
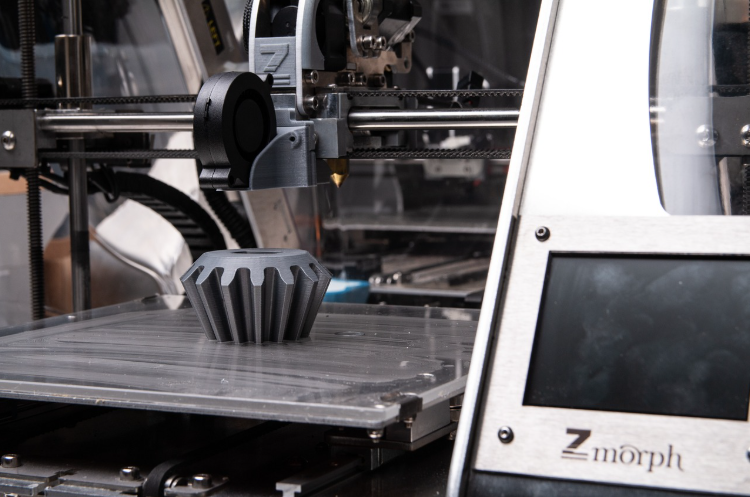
With the continuous advancement of technology, 3D printing is transforming the design and production processes of the jewellery industry. This technology, also known as additive manufacturing, involves creating three-dimensional objects layer by layer from a digital model (Sadiku, Olaleye, & Sadiku, 2025).
In contrast to traditional jewellery-making methods, which typically rely on handcrafting and casting, 3D printing offers a more flexible, precise, and cost-effective approach. It encompasses everything from rapid prototyping to streamlined manufacturing, enabling designers to quickly test multiple iterations and significantly reduce the time needed to turn a concept into reality. Unlike traditional model casting, 3D printing allows for the batch production of unique jewellery pieces while eliminating the processes of creating wax models, making moulds, and casting metal, which saves valuable time (Jaeger, 2023).
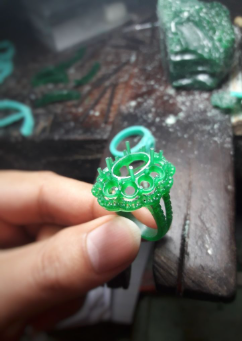
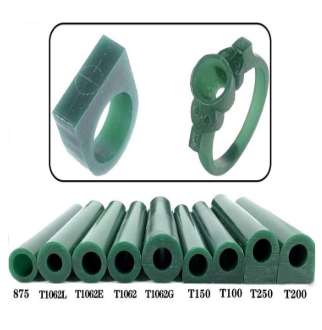
When discussing 3D printing in the jewellery industry, two main methods are typically used: direct 3D printing and investment casting. Direct 3D printing involves printing the final piece directly using metal or plastic, while investment casting involves 3D printing a wax model, which is then used to cast the final piece. To produce prototypes, jewellery manufacturers have adopted various 3D printing methods, including digital light processing (DLP), selective laser sintering (SLS), and fused deposition modelling (FDM) (Sadiku, Olaleye, & Sadiku, 2025). Each method offers unique advantages in terms of material compatibility, precision, and production speed, enabling jewellery designers to experiment with innovative designs while optimizing their workflow.
The applications of 3D printing in the jewellery industry:
- ● Prototyping and Concept Development: 3D printing allows jewellers to quickly produce prototypes, enabling them to visualize and refine designs before final production. This accelerates the iterative design process, allowing for faster experimentation and decision-making.
- ● Mass Customization: By combining batch production with individualized customization, 3D printing provides a high level of flexibility in manufacturing. It enables jewellery pieces to be personalized while maintaining the efficiency of mass production.
- ● Direct Manufacturing: Direct 3D printing uses laser and powder bed fusion techniques to sinter metal powder particles together, enabling the creation of complex, high-precision jewellery pieces directly from digital files. This method allows for more intricate designs and greater control over the manufacturing process (Jaeger, 2023).
- ● Investment Casting: Investment casting, which involves creating a wax model for casting, can produce extremely detailed and complex designs. This process ensures the precision and fine detail required for high-quality jewellery components.
In jewellery production, 3D printing enables cost-effective small-batch or even one-off production. This technology greatly simplifies the production process, accelerates delivery times, and allows brands to quickly respond to market trends and consumer demands. Additionally, 3D printing ensures high precision, meaning the final product closely matches the original design specifications. This level of accuracy is crucial for jewellery, where fine details and intricate craftsmanship are essential. By lowering production costs and making small-batch production feasible, 3D printing empowers even smaller jewellery brands to create high-quality, customized pieces.
However, despite its many benefits, 3D printing does present some challenges. For instance, 3D printers, especially those used for metal printing, are typically expensive. Although these printers can save production costs in the short term, the initial investment and ongoing maintenance fees may be unaffordable for many small jewellery brands or independent designers. Additionally, while 3D printing reduces material waste during production, certain materials used in the printing process, such as plastic, can have a negative environmental impact. Therefore, jewellery brands must carefully consider the advantages and limitations of 3D printing, balancing cost, production efficiency, and environmental factors.
In conclusion, 3D printing is fundamentally transforming the jewellery industry. It is making the production process faster, more customizable, cost-effective, and sustainable. By providing designers with greater creative freedom and offering consumers more personalized options, 3D printing is revolutionizing how jewellery is designed, produced, and consumed.
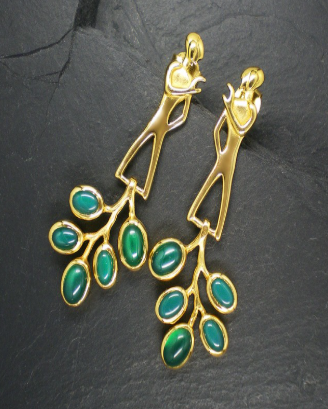
Ready to know more?
Visit us at the Malaysia International Jewellery Fair (MIJF) on 27 – 30 June 2025! Explore this renowned jewellery fair in the Southeast Asia region, featuring fabulous collections from shimmering diamonds to dreamy gemstones. Stay tuned for more updates!
References:
Sadiku, M. N. O., Olaleye, O. D., & Sadiku, J. O. (2025). 3D printing in jewelry. International Journal of Trend in Research and Development, 11(4), 123-130. https://www.ijtrd.com/papers/IJTRD28448.pdf
Jaeger, N. (2023, November 27). 3D printing jewelry – The ultimate guide. All3DP. https://all3dp.com/1/3d-printing-jewelry-the-ultimate-guide/